When any lab hires a new employee, they must receive a lab safety orientation training. Lab safety orientations cover important safety plans and procedures. These include the facility’s Chemical Hygiene Plan, Emergency Action Plan, decontamination protocol and Bloodborne Pathogen Biosafety Plan, wherever applicable. Depending on the employee’s work history, they may have experience with several orientation trainings in the past. Of course, this likely means they have experience with similar topics. As a result, lab training materials can feel stale, or lose their appeal.
So, how do you produce an engaging training while covering baseline material? One way is to ensure that your lab’s safety trainings have critical information that’s new and relevant. In this post, we’ll discuss three essential topics to implement into lab safety trainings.
1. Current Safety Culture
Discussing gaps in the lab’s current safety culture puts focus on key areas for improvement. Also, they help set safety goals within a lab. Gathering opinions of current employees during trainings, while using data from routine lab inspections, can point to certain trends. These include how often proper PPE is not in use. Or, they’ll help employees work towards performing their jobs safely and effectively.
Similarly, safety trainings provide an opportunity to highlight consistent strengths in workplace safety culture. This encourages employees to keep up the good work. Ensuring lab employees of any position are conscious of current safety goals can drive a positive shift in an organization’s overall safety culture. As a result, this will keep employees engaged during safety trainings.
2. Past Violations and Incidents
Most EHS departments regularly track and keep record of any violations, incidents, chemical spills or accidents that occur onsite. Incident reports include thorough analysis into why and how the incident took place. Also, they can provide a real-life example of what can happen if there’s a lapse in safety measures on site.
Use these records from audits and inspections to discuss past incidents and outline what steps could be taken to reduce risk of a similar issue in the future. Discussing these past incidents will help the employee have a better understanding of the safeguards that are already in place and why they are important.
3. Data Changes
The metrics discussed during safety trainings are constantly changing. Lab safety is a moving target, so explaining which metrics are most important to the team’s safety initiatives and why helps ensure all employees are working towards the same goals. If these goals change, employees should be kept up-to-date during refresher trainings. Outlining new safety goals and what metrics will track progress can help keep safety trainings fresh and engaging.
Orientation trainings are mandatory. However, ensuring the trainings are up to date, relevant, and engaging is imperative to delivering effective safety training, so your operations can run smoothly. While adding questions throughout trainings keeps employees engaged for the moment, adding timely data can help keep important information from the trainings top of mind in the workplace.
Conclusion – SEPS
SEPS’s experts can provide comprehensive support for your organization’s lab and facility needs. By supporting your lab’s safety and sanitation, we’ll help you cultivate a workplace of maximum safety and efficiency. Whether you need assistance optimizing your equipment or maintaining high standards, our accreditations and affiliations are a testament to our expertise and professionalism.
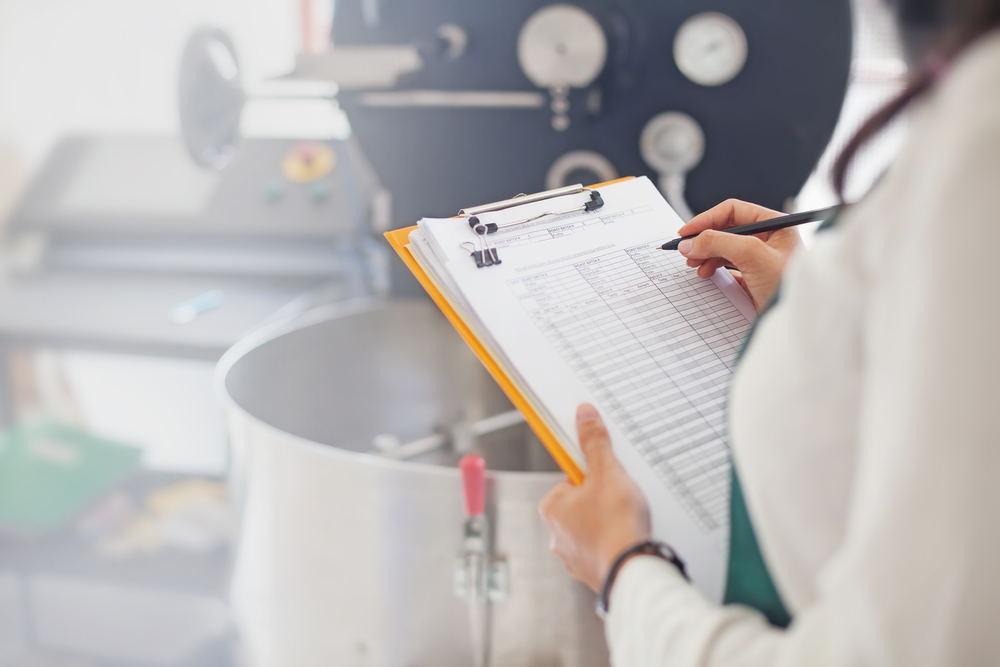