Managing a lab these days is a spectacular balancing act. At SEPS, we’re experts on helping to keep labs clean, safe and functional. Hygiene, equipment operating, maintenance and repairs demand constant attention. And considering our decades of experience, plus varied repair and certification services, we know all about how to maintain a lab.
Of course, the modern lab needs regular administrative attention. And this is true within all industries – whether it’s scientific, food research, pharmaceutical or medical. In this post, we’ve collected some essential guidelines directly from industry experts discussing how to prevent contamination and keep your lab safe, hygienic and functional. Regardless of your field, these can help keep your lab cost-efficient and make daily operations a lot less stressful.
1. Maintain Your Direct Workspace
Basically, this is the most rudimentary start to effective lab maintenance. Often, it’s easy to overlook in high-volume and fast-paced work environments. However, we don’t realize just how critical it is to maintain the space in which you’re working every single day.
Of course, this entails keeping your desk, tabletop or direct workspace clean. And not just clean, but clear, organized and sterile. In between tasks, dispose of trash and sanitize the communal instruments that everyone handles. Designate storage spaces for items that wastefully occupy unnecessary space and interfere with your work. You should take additional steps to ensure you’re properly sanitizing high-traffic areas.
Mostly, lab work is visual. Additionally, much of it involves observations, readings and data. Therefore, if you can’t see your work clearly, it presents an incredible challenge. Keeping your lab well-lit is just as important as keeping equipment working. Task lighting provides an energy-efficient way to illuminate your space and streamline your work. You can keep your lighting systems functional with repair services in the event they’re malfunctioning.
Understandably, you may consider this obvious advice. However, you’d also be amazed how often many labs overlook it. Simple clutter and disorganization can lead to graver problems for your lab. In fact, many of the serious issues our team is called in to fix began as simple ones that could’ve been easily avoided.
The best way to accomplish this is by developing a routine with assignments to each worker. Keeping your lab well organized, decluttered, and sanitary is the first step to smooth operations.
2. Preserve Your Equipment
You may think this one’s out of your control. However, that’s certainly not true. Lab equipment is very expensive, and often very fragile. But luckily, there are some foolproof ways to prevent any costly and inconvenient disrepair.
Usually, each lab worker uses most (or all) of the equipment. Basically, that enhances the inherent risk of contamination and disrepair. Therefore, this is where the cleaning and organization can be very beneficial for everyone. All lab personnel should have some degree of responsibility for keeping equipment clean and sterile.
In addition, it’s important to understand your equipment’s mechanics. This is why the paperwork that manufacturers provide should always be kept in a designated location. As a result, when someone needs it, they can easily consult it. The paperwork that comes with your equipment is basically a complete guide to keeping it operating smoothly. By learning these specifications, you’ll be saving yourself a lot of future stress.
For your equipment, regular and thorough cleaning is essential. Schedule in-depth cleaning, decontamination and certification once every three to six months. Also, while cleaning your equipment is important, calibrating it is vital, too. It will substantially increase the life of machinery. Of course, it will also keep your employees safer. Equipment that hasn’t been calibrated properly can have much bigger problems than disrepair. If it hasn’t been calibrated, it can sometimes injure lab personnel or damage nearby equipment.
3. Make Sure It’s Certified!
Whether you work in a cleanroom or use equipment like fume hoods, biosafety cabinets or any fan/filter unit, certification is crucial. Since we specialize in procedures like certification and more, we understand their importance.
Lab equipment certification involves specially engineered tools and expert technicians. Specialists conduct rigorous tests to verify that everything is operating correctly. Certification is a way to reliably confirm the quality of your lab and its equipment.
It’s critical to make sure your equipment and work environment are both functioning properly. Also, it’s important to keep the certification documents stored in a designated location.
Conclusion
Laboratories are often the primary frontiers for scientific innovation. Extraordinary work is regularly accomplished in labs. Naturally, ensuring they function well can sometimes be demanding.
However, it’s also entirely possible to keep your lab running smoothly and efficiently. Keeping these tips in mind can prevent costly and time-consuming problems from arising. Cleanliness, organization, and certification are all proven ways to keep your lab hygienic and functional. At SEPS, our accreditations and affiliations are a testament to our enduring commitment to helping labs achieve this.
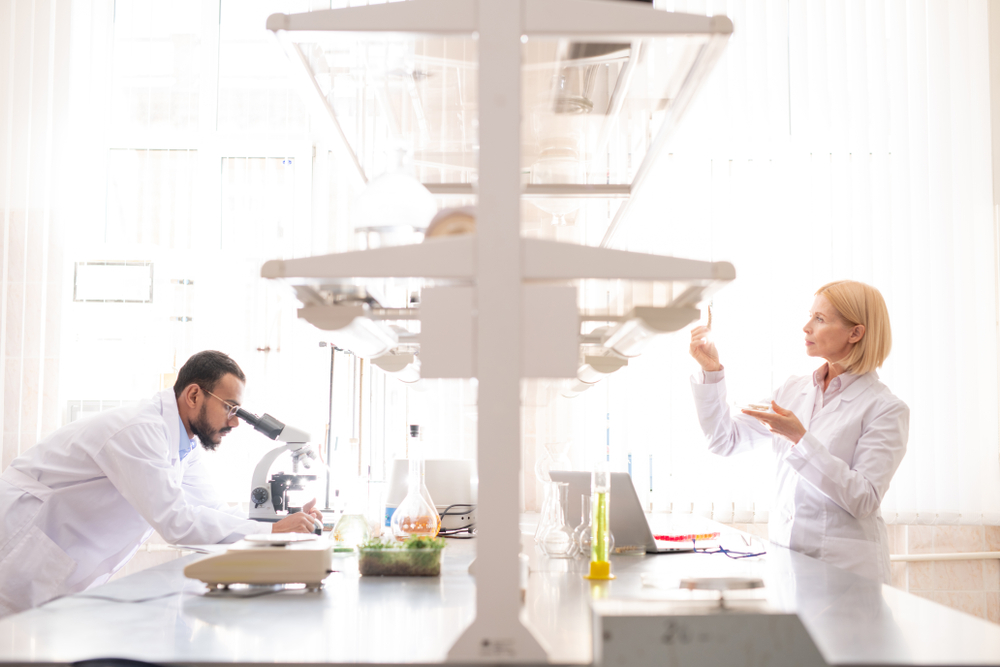