A biological safety cabinet is one of the most important tools for the countless labs that use them. At SEPS, biological safety cabinets (or BSCs) are one of the lab tools we have the most experience cleaning, repairing and maintaining. They’re critical to preserving the safety of lab workers. Nowadays, in the age of COVID-19, these units are more important than ever. In addition, they’re equally as vital to the quality of your work and research.
Obviously, the presence of a biosafety cabinet is critical to general worker safety. However, it’s equally as important to implement cleaning and decontamination practices in every lab that uses them. While they will keep hazardous pathogens away from employees, it’s up to staff to ensure they’re well maintained. But how do you go about it? How do you keep them as safe and sanitary as possible? In this post, we’ll break down the essential checklist for decontaminating your biosafety cabinet.
About Biosafety Cabinets (BSCs)
Any lab with a biosafety rating is likely to have a biosafety cabinet in their workspace. A BSC is an enclosed, ventilated space in which employees can handle dangerous (sometimes lethal) samples and materials safely. HEPA fan and filter units direct and filter air away from lab personnel.
Biosafety cabinets come in three different classifications: 1, 2 and 3. Class 1 cabinets protect the workers and their immediate surroundings. Class 2 cabinets protect the user, their environment and the sample in question. Finally, Class 3 provides the most possible protection. Usually, workers are handling materials with a biosafety rating of 4, the very highest rating, in a Class 3 cabinet. It is a gas-tight enclosure in which workers must reach through a “glove box” in order to manipulate the sample.
Decontamination Checklist
Since biosafety cabinets are integral to work and research, it’s vital to decontaminate them after every use. Below, you’ll find the most important decontamination steps your employees should take following each use.
First, put away anything which may have been in contact with the materials. Also, be sure to cover any waste containers. Be sure to let the BSC run for about five to ten minutes with zero work or activity. This will ensure that the fans and filters purge contaminants from the unit.
Next, be sure to clean and disinfect absolutely all tools, equipment or containers. Then, remove them from the biosafety cabinet. You should set aside at least thirty minutes for properly disinfecting every work surface within the cabinet. Pay special attention to the back, sides and the inside of the glass.
Also, if you’re using a particularly abrasive cleaning agent (or chloride-type disinfectant), wipe each surface with a 70% alcohol solution. Many labs overlook this step. Unfortunately, forgetting this step can seriously compromise the interiors. If your BSC is made of stainless steel, it will begin to corrode and likely cause irreversible damage.
If any workers change gloves, be sure to implement a stringent hand-washing policy. Failing to do so can lead to serious cross-contamination between surfaces. If any employees spill chemicals or fluids, wipe them with a paper towel. Then, immediately place them in a biohazard bag for proper disposal. In some cases, you should monitor the biosafety cabinet for radioactivity. Obviously, this depends on the work in question. If your lab doesn’t handle any radioactive materials, then this step is clearly unnecessary.
This very simple care and maintenance can go a very long way towards keeping your lab and its employees safe.
Conclusion – SEPS
At SEPS, lab safety and sanitation is our very highest priority. In addition, we make it our mission to help labs in all industries maintain exemplary standards. Biosafety cabinets are one of the most important tools for keeping workers safe. Therefore, we offer a wide range of services to certify that yours is operating as safely as possible.
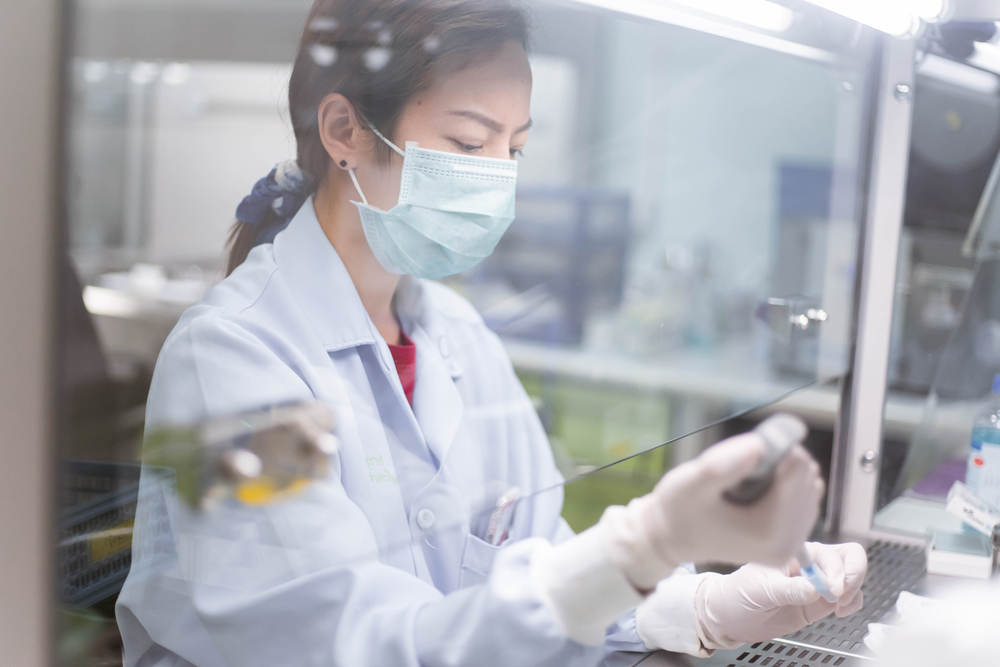